In honor of our conference on digital manufacturing, The Digital Factory, Formlabs is releasing a limited-run podcast! In this series, hosted by O’Reilly Media’s Jon Bruner and guest host David Cranor, we’ll explore the future of the factory floor through conversations with experts who are changing the way things are made.
In episode 3, we sit down with Spencer Wright, head of product at nTopology, where he helps build software that generates specialized lattices suited for specific manufacturing constraints. Wright also authors The Prepared, a weekly newsletter covering manufacturing, engineering, and infrastructure from an accessible human perspective with as much of a focus on societal implications as on technology.
Play the full podcast to hear:
- The challenges and rewards of moving from traditional machining to metal 3D printing.
- The benefits of lattice structures and how they’re generated.
- The potential downsides of an automated future.
The Digital Factory Conference is returning to Boston on May 7, 2019. Jeff Immelt hosts, and speakers include the CEO of Align Technology, CIOs of FedEx and Baker Hughes, the head of manufacturing at Ford Motor, CTO of GE, and CEOs of Formlabs and Desktop Metal. Visit thedigitalfactory.com to see the program, and register soon; prices increase as the conference approaches.
- Listen on iTunes
- The Prepared: Spencer Wright’s Newsletter
- Spencer Wright on Twitter
- Jon Bruner on Twitter
- David Cranor on Instagram
- Formlabs on Twitter
Exploring the Future of Low-Volume Production
In this episode, we discussed some of the barriers to more localized, low-volume production of functional parts–and some of the trends already in motion that could break those barriers down.
On the State of Metal 3D Printing:
“The metal printers on the market today cost up to about a million dollars, and they print parts smaller than a bread box. So, if you're looking for products that might work in those kinds of printers, they have to be relatively small, and they have to be relatively high value. You're looking for an industry where people are willing to spend a lot of money for relatively small increases in performance.
“These end up being great places to test ideas about the industry. You can sell relatively small volumes at relatively high prices, and you can get performance benefits from it.”
On the Transition From Machining to Metal 3D Printing:
“What I found, through my own exploration with primarily metal 3D printing, is that this is a process. If you design a part that comes from a machining background or a casting background, put it in a 3D printer, and press go, you get bad results on a couple of different metrics. As I was exploring my own research in metallurgic manufacturing, I became more and more interested in new design techniques that are really specifically for industrial 3D printing.
“There are general purpose CAD suites, things like Inventor, and SolidWorks, and Fusion, and higher end packages like Siemens NX or PTC Creo. They're fantastic, but they're not particularly good at niche manufacturing processes that have specific design constraints. So, with metal 3D printing, there are all these different reasons why you would want to create these really complex lattice structures, and it's very difficult to do so with traditional CAD software.”
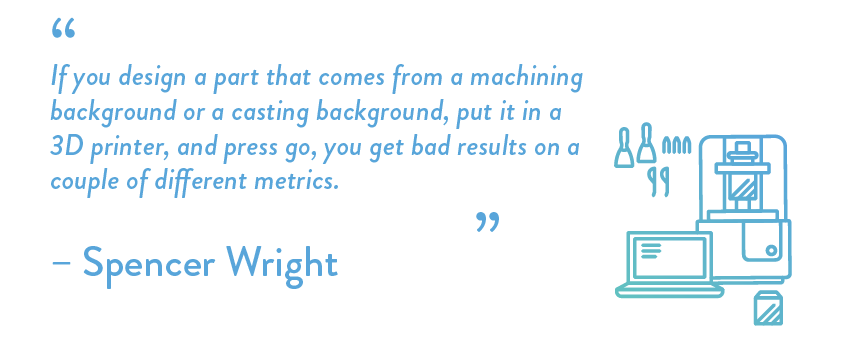
On the Challenges of Working With Job Shops for Small Runs:
“Getting job shops to take you seriously is hard. It doesn't matter how you're manufacturing things. If you're ordering in bulk, people are still going to give you a discount because their sales team has to work that much less hard in order to get enough business.
“If you're just buying one part, getting a job shop to take you really seriously, and to work through what is ultimately a complex engineering challenge, can be really hard. Whereas if you come to them and say, ‘Hey. This thing that I'm making, I'm going to order 20,000 of them next year,’ if they believe that, they're going to take you very seriously.”
On the Power of Cross-Pollination and the Downsides of Automation:
“We're putting a lot of energy into automating this stuff, and for many of the problems in engineering and manufacturing today, that's a great idea. That's fantastic for a huge portion of CNC machining, but I do think that there's value to sitting in the same room as somebody who's running a machine. I think it's really valuable to have run a machine at some point yourself.
“I worry sometimes that if we go 100 percent in that automated direction, then is there a downside to that? Do we lose all chance of having the kind of Shenzhen ecosystem where there is that proximity, and there is that cross-pollination too? Automate all you want, but I think that there is some place for communication across disciplines, and I'm not sure that we've figured out software solutions to do that in any context.”
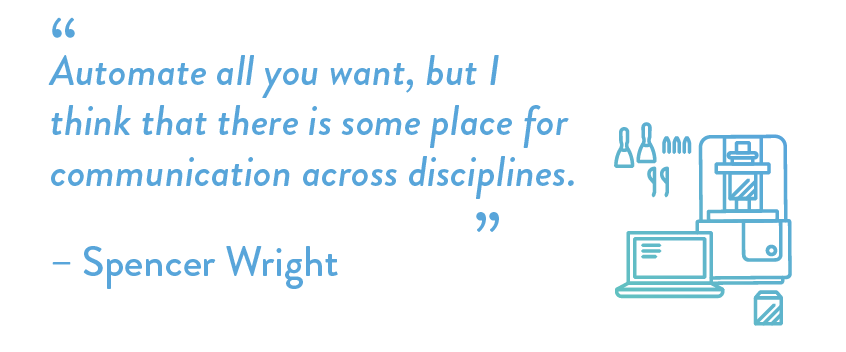
On the Aesthetics of Lattice Structures:
“We work with a couple of different consumer tech companies, and one of the places that we've seen lattices a lot over the last few years is in shoes. There, you're getting a combination of two effects. On one hand, they do have a visual component, and you're actually looking at it. Similar to the way that the air pocket on Nikes became such a huge deal, we're seeing kind of a movement where, instead of having a foam mid-sole, you have a full lattice structure. It’s visually interesting, and it also provides really unique cushioning characteristics. So maybe the heel of your shoe is going to have a different density and a different response rate than the toe is, or something like that.
“The people that use lattices in the most visually striking way to my eye are Nervous System out of Boston. They make really beautiful jewelry and textiles. It's kind of a weird application of textiles, chainmail textiles. Which sounds cold, but it's actually really amazing.”
The Future of the Factory Floor
Stay tuned for the next episode of the podcast in a few weeks! In the meantime, you can access talk recordings and our Digital Factory podcast archive on the Digital Factory website.
- The Future of Making Things, Carl Bass, Autodesk
- From Moore's Law to Lass' Law, Neil Gershenfeld, Center for Bits and Atoms, MIT
- CAD in the Cloud, Jon Hirschtick, Onshape
- Gap-to-Zero: The Next Revolution in Manufacturing, Suchit Jain, SolidWorks
- And more!