In honor of our conference on digital manufacturing, The Digital Factory, Formlabs is releasing a limited-run podcast! In this series, hosted by O’Reilly Media’s Jon Bruner and guest host David Cranor, we’ll explore the future of the factory floor through conversations with experts who are changing the way things are made.
In episode 4, we sit down with Ric Fulop, the founder and CEO of Desktop Metal, founded in 2015 with the goal of reinventing the way design and manufacturing teams print with metal. Like Formlabs, Desktop Metal is hard at work making industrial technology more accessible and bringing 3D printing further into the realm of production of end-use parts.
Play the full podcast to hear:
- How Desktop Metal’s 3D printing process differs from powder bed fusion
- The details of the processes used to produce metal parts today
- The technical details of Desktop Metal’s studio and production systems
The Digital Factory Conference is returning to Boston on May 7, 2019, and Ric Fulop joins the program for a second time. Jeff Immelt hosts, and speakers include the CEO of Align Technology, CIOs of FedEx and Baker Hughes, the head of manufacturing at Ford Motor, CTO of GE, and the CEO of Formlabs. Visit thedigitalfactory.com to see the program, and register soon; prices increase as the conference approaches.
- Listen on iTunes
- Ric Fulop on Twitter
- Jon Bruner on Twitter
- David Cranor on Instagram
- Formlabs on Twitter
Reinventing Metal 3D Printing
In this episode, we explored Desktop Metal’s studio and production systems and how they’re working to expand the metal 3D printing market.
On the Current Metal 3D Printing Market
“Today, you have people that print metal parts, but [the machines] are really inaccessible. There are only about a billion dollars worth of metal machines, and the average machine installed is about a million dollars. Printing of metal parts is still in its infancy, and it's a very, very small market compared to metal parts as a whole.
“The reason why it's a small market is because the technology is not accessible, and it's too hard to use, and it's too expensive for use in production. As a result, the only people that make parts that are 3D printed with metal today are industries like aerospace where they're able to pay very high price or industries like implantables in medical.”
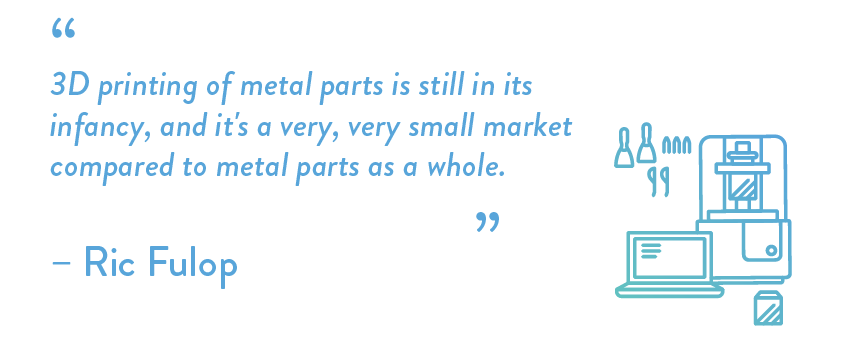
On the Fundamentals of Desktop Metal’s Process
“Our printer uses a media that looks like a crayon. We bound all the metal powder in a polymer matrix, over a variety of polymers, and then that is extrudable. It works the same as a fused deposition modeling (FDM) printer, but you can make metal parts. Then we have a second process where a microwave and a sintering system sinter the parts into a fully dense metal object. Those two parts give you our studio system, which is, in reality, the first office friendly metal printer in the market.”
On the Pervasiveness of Metal Injection Molding
“Metal injection molding technology is in every cell phone and in every laptop and in every car and in every medical device tool. It's how you make highly complex, small parts. Billions of parts a year. Every time you have a flex connector inside a laptop, the little metal part at the end that attaches or mates it to the rest of the chassis would be metal injection molded. Parts of your Apple Watch or Lightning Connector in those systems are metal injection molded.”
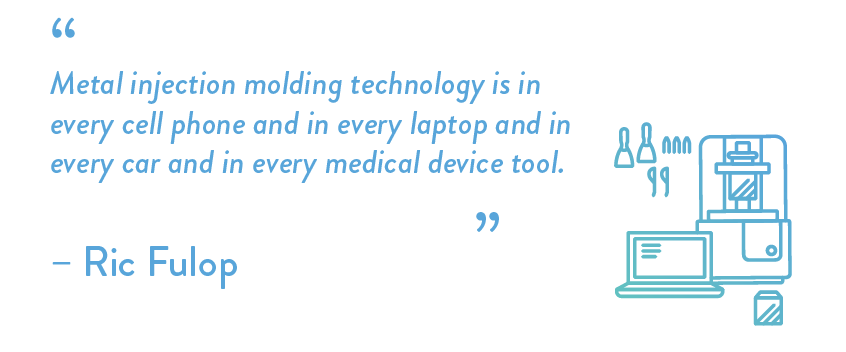
On the Difference Between Sintering and Melting
“Melting occurs once you've reached the melt state of the material and you have a phase change and, in the case of metal, it becomes liquid. When you're sintering materials, it's a different process. Things have lots of different particles and you put them together and as you raise the temperature, the particles want to attract to each other and the pores between the particles close and the part consolidates together until it is at full density. It's a different process to densify materials.”
On The Single Pass Jetting Process
“The industrial machine uses a process we call single pass jetting, and it works by basically having two powder spreaders that move bidirectionally in two directions. The first print bar lays down a binder, the second print bar lays down the ceramics so you that you have interfaces for supports, and then you move them in opposite directions. You move in one direction, print and spread powder, second direction, spread powder and print. You’re moving back and forth, nonstop, every second and a half or so, doing 50 microns.”
The Digital Factory Conference returns to Boston on May 7, 2019! Visit The Digital Factory for an archive of talks, podcasts, and more from experts at the forefront of digital manufacturing, and to register to attend our next event.